NL-Series
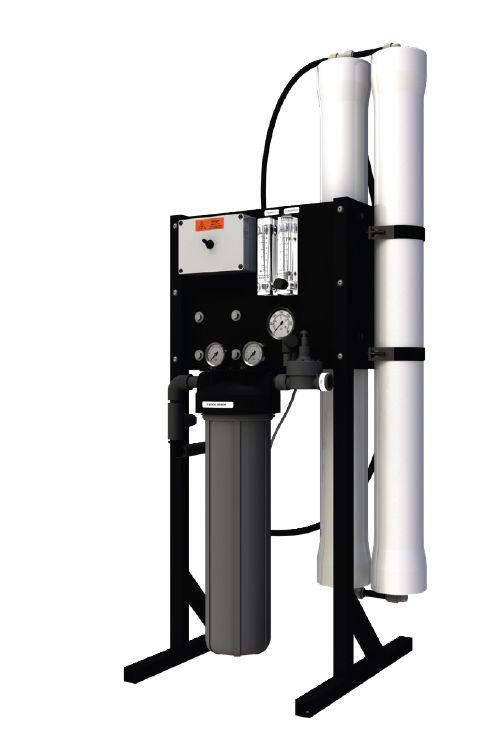
NL – Series Membrane Systems are available in capacities of 2,000 and 4,000 gallons per day. These commercial RO systems come equipped with a high-pressure pump and the necessary components for application flexibility, ease of use and economical design.
Benefits
• Simple On/Off controller
• Compact Design
• Instrumentation Easily Accessible
• Pre-Plumbed, Wired and Assembled
• Easy Maintenance and Servicing
• Low Operating and Maintenance Costs
• Individually Tested
• 1-Year Limited Warranty
• Assembled in the USA
Features
• Simple On/Off controller
• Permeate Flow Meter
• Concentrate Flow Meter with Integrated Stainless
Steel Needle Valve
• Pre and Post Filter 0-100 psi Glycerin Filled Gauges
• XE2–Series 4” x 40” Membrane
Elements (70 psi)
• FRP Membrane Housings
• SDF– Series 4.5” x 20” Diameter 5-Micron
Sediment Pre-Filter
• Pentair® Big Grey Filter Housings
• Flotec® Booster Pump
• Chemical Injection Port and Electrical Connection
• Normally Closed Composite Feed Solenoid Valve
with Bypass
• Stainless Steel Throttle Valve
• Feed Low Pressure Switch
• Parker®/Seatech® Push/Pull Quick Connect Fittings
• Black Powder Coated Aluminum Frame
Specifications
Test Parameters: 500 TDS Filtered (5-micron), Dechlorinated, Municipal Feedwater, 65 psi / 4.50 bar Feed Pressure, 70 psi / 4.8 bar Operating Pressure, 77°F / 25°C, Recovery as stated, 7.0 pH. Data taken after 60 minutes of operation.
A. Low temperatures and feedwater quality, such as high TDS levels will significantly affect the systems production capabilities and performance. Computer projections must be run for individual applications which do not meet or exceed minimum and maximum operating limits for such conditions.
B. Product flow and maximum recovery rates are based on feedwater conditions as stated above. Do not exceed recommended permeate flow.
C. Varies with motor manufacturer.
D. Does not include operating space requirements.
Operating Limits
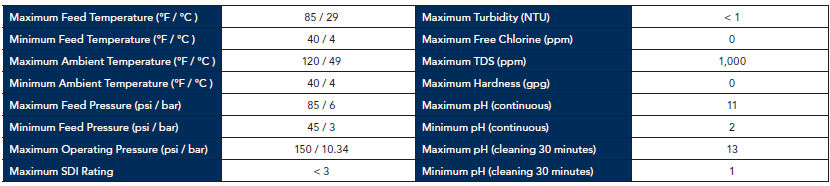
R1-Series Membrane System
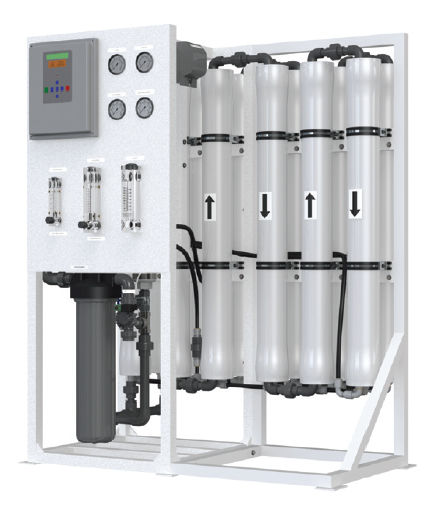
R1– Series Membrane Systems are designed for overall superior performance, high recovery rates, minimal energy consumption and offer great savings with low maintenance and low operation costs.
R1– Series Membrane Systems feature
a new, innovative design. These systems feature
only the highest quality components, including a
programmable computer controller with many builtin
standard features, a stainless steel booster pump
for high performance and corrosion resistance, ultra
low energy membranes and fiberglass membrane
housings for enhanced performance and durability.
R1– Series Membrane Systems have been
engineered for capacities ranging from 1,800-21,600
gallons per day.
Benefits
• Fully Equipped and Customizable
• Skid Mounted
• Decreased Size of Dimensional Footprint from Standard Membrane Systems
• Components Easily Accessible
• Pre-Plumbed, Wired and Assembled
• Individually Tested and Preserved
• Low Operation and Maintenance Costs
• Easy Maintenance and Servicing
• 20% Less Energy Use than Standard Membrane Systems
• 1-Year Limited Warranty
Features
• S–150 Computer Controller
• LCD Backlit Display
• Pre-Treatment Lockout
• Tank Level Input
• Low Pressure Monitoring and Alarm
• Hour Meter
• TDS Monitoring
• Feed Flush
• Permeate and Concentrate Flow Meters
• Concentrate Recycle Flow Meter
• Pre-Filter 0-100 psi Panel Mounted Glycerin Filled Gauges
• Pump Discharge and Concentrate 0-300 psi Panel Mounted Glycerin Filled Gauges
• 5-Micron Sediment Pre-Filter
• HF5 – Series Ultra Low Energy Membrane Elements
• FRP– Series Membrane Housings (300 psi)
• by Pentair® 20" Big Grey Cartridge Housings
• Goulds® Multi-Stage Stainless Steel Booster Pump
• ASCO™ Composite Feed Solenoid Valve
• Feed Low Pressure Switch
• White Powder Coated Aluminum Frame
• Dual Chemical Pump Outlets
Options and Upgrades
• S–150 Expander Board
• S–150 Dual TDS Board and Sensor
• Filmtec® LCLE Membrane Elements
• SS–Series Membrane Elements
• NF3–Series Membrane Elements
• NF4–Series Membrane Elements
• HR3–Series Membrane Elements
• Hanna® BL 981411 pH Controller
• Permeate Flush
• Permeate Divert
• Permeate Sample Valves
• Pump Pressure Relief Valve
• Blending Valve
• High Pressure Tank Switch
• Wooden Crate
Specifications
Test Parameters: 550 TDS Filtered (5–Micron), Dechlorinated, Municipal Feedwater, 65 psi / 4.50 bar Feed Pressure, 80 psi / 5.5 bar Operating Pressure, 77°F / 25°C, Recovery as stated, 7.0 pH. Data taken after 60 minutes of operation.
A. Low temperatures and feedwater quality, such as high TDS levels will significantly affect the systems production capabilities and performance. Computer projections must be run for individual applications which do not meet or exceed minimum and maximum operating limits for such conditions.
B. Product flow and maximum recovery rates are based on feedwater conditions as stated above. Do not exceed recommended permeate flow.
C. Varies with motor manufacturer.
D. Does not include operating space requirements.
Operating Limits
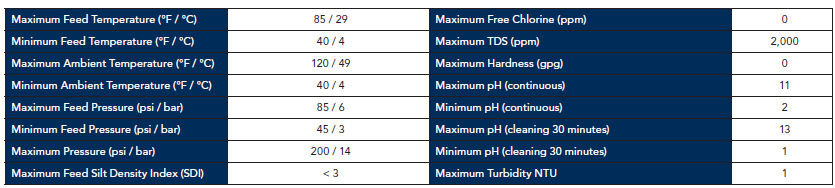
X-Series Membrane System
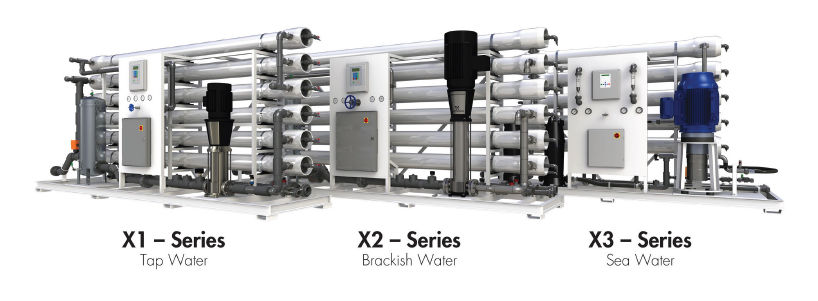
X – Series Membrane Systems utilize reverse osmosis technology to produce high purity water by reducing
contaminants such as dissolved minerals, particulates and organic impurities. X – Series Membrane Systems are
engineered using the highest quality components and materials for reliable operation and exceptional performance.
Our standard systems are available with product water outputs from 6 – 396 gpm (8,640 – 570,240 gpd).
X – Series Membrane Systems are offered with a variety of options such as pre– and post–treatment equipment, distribution pumps and integrated controls for a complete water treatment solution. X – Series Membrane Systems are skid mounted, pre–plumbed and pre–wired allowing for quick installation and start up. A variety of membrane types are available including low energy, brackish, sea water and low fouling, nanofiltration and ultrafiltration. Our engineers are available for consultation and to assist you in designing your next water treatment solution.
The following are just a few of the industrial
applications that benefit from the use of an
industrial membrane system:
• Boiler Feedwater
• Small Municipalities
• Chemical Manufacturing
• Electronics Manufacturing
• Metal Plating and Finishing
• Ink and Dye Production
• Ice Production Equipment
• Food and Beverage Production
• Bottled Water
• Deionization Pre–Treatment
Features Overview
SKID AND FRAME ASSEMBLY
Membrane systems are manufactured in a skid frame
design for ease of installation with minimum floorspace
requirements. X – Series Membrane Systems are
constructed of welded structural carbon steel tubing and
finished with corrosion resistant epoxy powder coating.
Stainless steel fasteners and hardware is standard for
added corrosion resistance.
CARTRIDGE PRE-FILTRATION HOUSING
Integrated prefiltration is standard on all systems.
SYSTEM PRESSURE PUMP
Standard pressure pumps are constructed with 304 / 316
stainless steel housings, as well as impeller and diffuser
stage assemblies. Pumps are equipped with TEFC motors
and wired for 230 / 460 VAC voltage, and rated for full
load, continuous duty.
MEMBRANE HOUSINGS
All systems feature membrane housings constructed of
fiberglass reinforced polyester (FRP) with 316 stainless
steel side–entry feed and concentrate ports. Standard
housings have a white polyurethane finish and are NSF61
rated. ASME code–stamping is available on all membrane
housings.
INSTRUMENTATION
All systems feature a complete instrumentation package
for optimal performance monitoring. Each of the
following instruments are panel–mounted and pre–wired:
• Pre– and Post–Cartridge Filter Pressure Gauges
• Pump Concentrate Pressure Gauges
• Inlet Pump Discharge Pressure Switches
• Permeate and Concentrate Electronic Flow Sensors or Rotameters
• Permeate and Feed Conductivity Monitor
• Temperature Sensor
• Pump Run Hour Meter
MEMBRANE ELEMENTS
Standard reverse osmosis membrane elements are high
rejection, thin–film composite (TFC) type, in a spiral–
wound configuration. Membrane elements are tested and
carry a one–year warranty against defects in quality and
workmanship.
SYSTEM CONTROLS
Operation of the systems are automatically controlled
through a comprehensive microprocessor controller
housed in a NEMA – 4X industrial electrical enclosure.
The control system also includes a pre–wired motor starter, operator switches, push–buttons, and status
alarm indicator lights. Standard systems include the
following isolated alarm conditions:
• Low Inlet Pressure
• High Pump Discharge Pressure
• High TDS
SYSTEM PIPING AND VALVES
All membrane systems are completely pre–plumbed and
installation ready. Sch80 PVC is used for all piping and
valves under 75 psig operating pressure. Higher pressure
piping and valves are constructed of 316 stainless steel
for the X2 and X3. The following valves are provided
as standard for accurate flow and pressure control and
convenient operation:
• Automatic Inlet Valve to Prevent Water Flow through the System During Shutdown
• Pressure Pump Discharge Throttle Valve
• Concentrate Valve
• Optional Recirculation Valve
• Automatic System Flush Valve for Prevention of Membrane Fouling and Scale Formation
• Inlet and Sampling Valves
• Individual Membrane Housing Product Sampling Valves
• CIP Ports for Use with Membrane Cleaning System
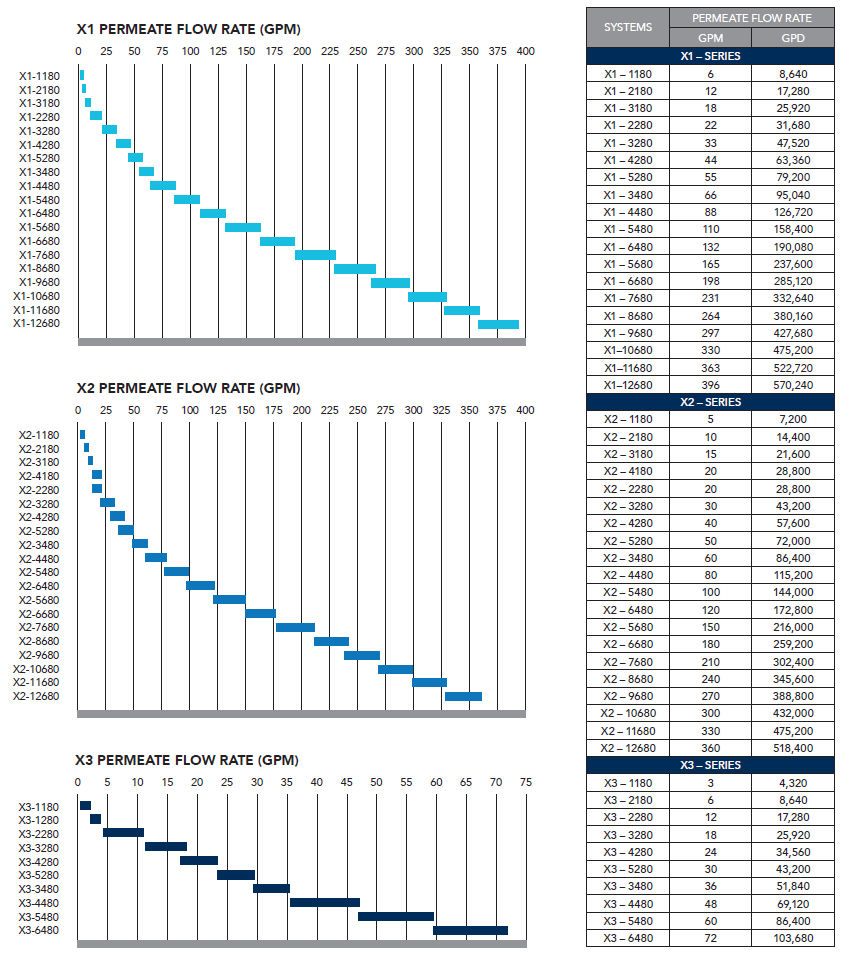